Pretty frantic weekend done on the car, didn’t take a huge number of photos because I’ve posted all this sort of stuff before and I just wanted to get it done!
With the box back in, I could start rebuilding the suspension and exhaust. The OS suspension I wanted to leave alone for a few more days, because I had some gearbox oil cooler parts coming from seriouslylotus and having the OS lower wishbone off the car would help with access.
There are a couple of approaches to gearbox cooling, a normal air radiator likely mounted either in a sidepod or maybe even horizontal to the floor by the sump would be slightly cheaper, but IMO would have had more mounting challenges. It’s also a ‘less regulated’ way of cooling, even though you can of course thermostatically manage the pump to mitigate that.
The other option, the way I wanted to go and the way seriouslylotus go with their kit is an air/water exchanger. The ‘cruising temp’ of the C64 gearbox is around the mid 80s which is also where the engine coolant spends much of its time on my car. On track my g’box temps got as high as 115 and increases got sharper and sharper the longer I was out on track so if I can take the edge off of it and allow for a more comfortable 25-30min session then that’s mission accomplished.
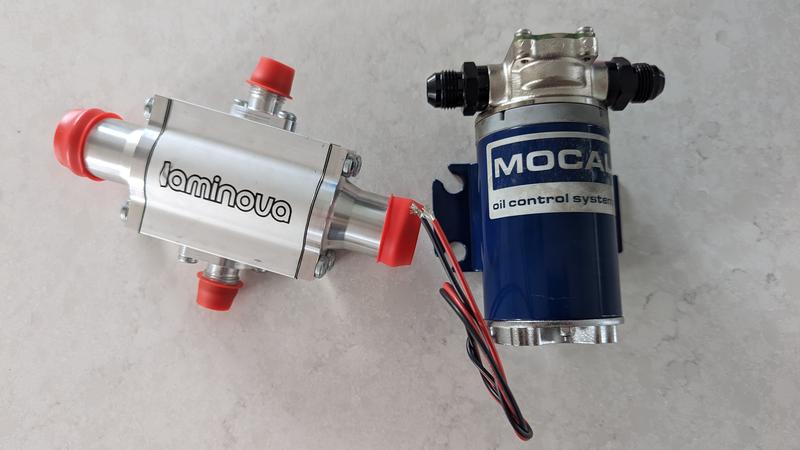
The Laminova is quite cute, I think it might be the smallest one that they do. The pump is a robust thing, it does apparently have a tendency to blow fuses if you try churning cold/stodgy oil through it so it’s not something you’d want to have running full time.
I’m not sure if I’ve plumbed this in the exact same way that SL would with their kits, but I opted to make my own oil lines so I could make it up as I went along. This was going to be my target water hose to splice into.
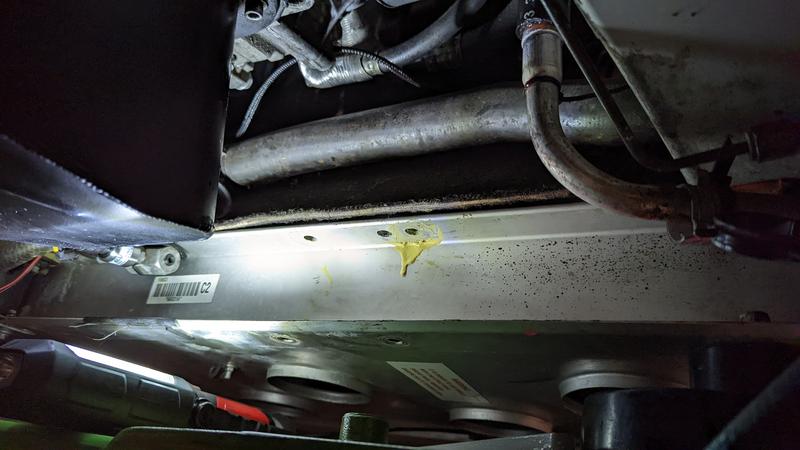
You can see the wishbone mount just below with the duralac leaking through, installing with the wishbone in place would be a bit more awkward than it was.
The oil lines would all be AN-8, so I put an order in for various fittings and a coil of braided hose and got cracking. It’s not the first time I’ve worked with AN- hoses, but it’s been a few years and it’s more difficult than I remember (or what Youtube will have you believe!). I woke up the morning after feeling like I’d done a stint in the gym (I guess?), very physical work to get them all pushed together!
It was ‘only’ 3 hoses, so the hard labour was relatively short lived. When I stopped fannying around desperately trying to not scratch the fittings I progressed much quicker, and actually ended up scratching them less. Figure that one out.
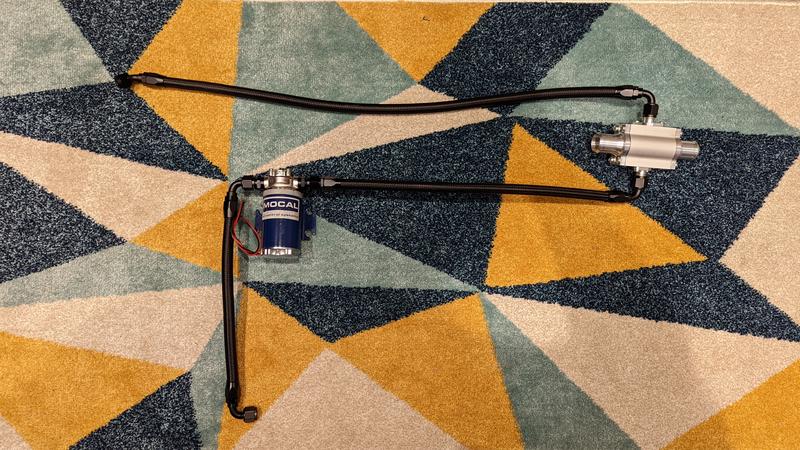
I nipped up the oil feed/return to the laminova before installation because it was going to be a bit tight in there, then threaded it all in. It’ll be fairly well obscured by an (engine) oil cooler line and heater hose once it’s in, but the jubilees are just about accessible and it’ll be easy to inspect for leaks etc.
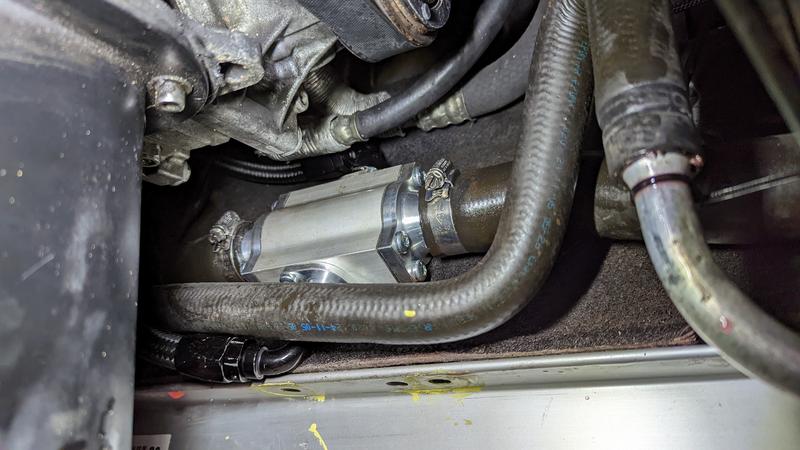
The pump itself is mounted on a plate which shares some bolts with the central engine mount and the NS wishbone mount.
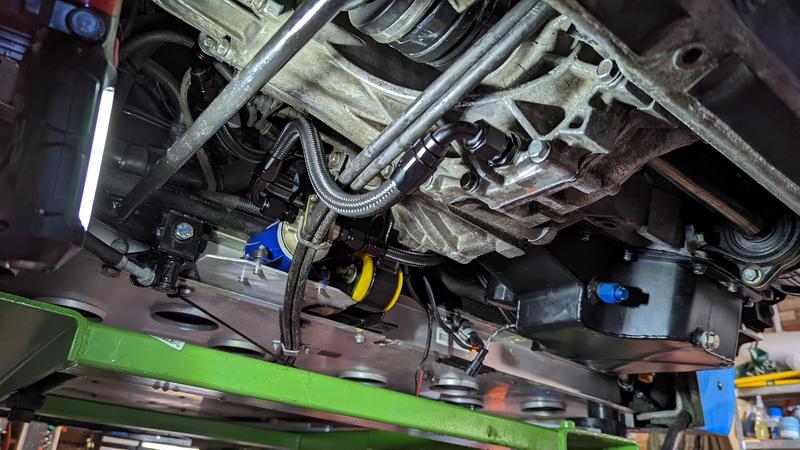
Gearbox drain and fill plugs are M18x1.5 so an easy size to buy AN-8 adapters for.
I’m pretty happy with my hose runs, enough “intentional” kinks in the hose to allow for engine movement, but they don’t really obscure any other service areas of the car so I don’t expect this install to annoy me later.
Finally the wiring, I ran this ages ago. As a reminder I’ve got 2x aux short to ground outputs on my ECUMaster ADU Dashboard. They run to a pair of fused relays in the boot, one of which then feeds my chargecooler pump and the other to this new gearbox oil pump. I can then use logic in the ADU software to trigger the pumps depending on whatever parameters I choose. The chargecooler will simply run whenever the ignition is on, but the gearbox pump will only run when gearbox oil exceeds a certain threshold. Currently 70 degrees, but I’ll play with it once I have some data to test with.
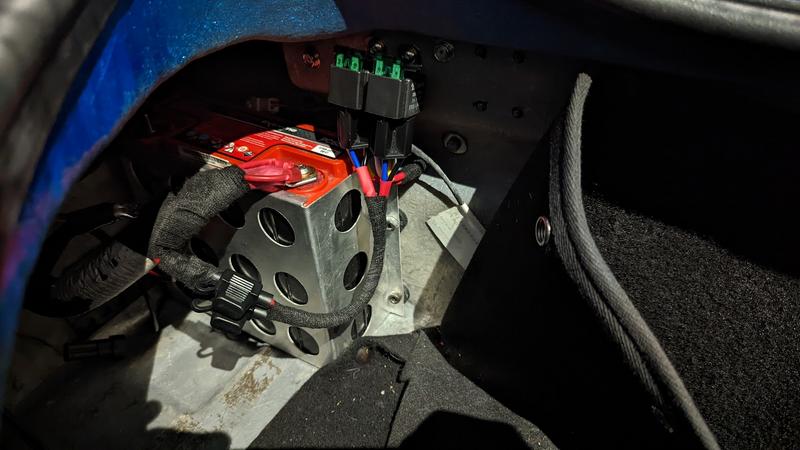
With a little telltale on the dash so I know when it’s active.
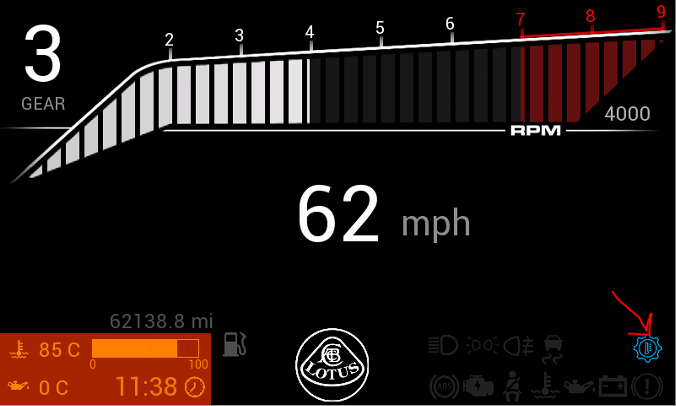
With all this in place, I filled the gearbox with oil (MT-90 again) and to help deal with my extra capacity I ran the pump for a couple of seconds to burp any air out, then topped back up again. I didn’t get that much oil in after the burping, so I may repeat this process after my first proper drive where the pump runs for a bit.
With that done, the rebuild could be finished off.
Exhaust on and sensors in.
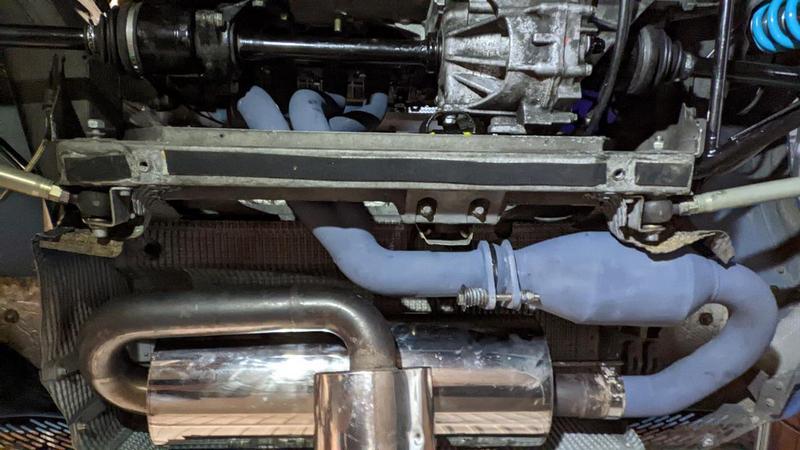
Suspension on with new brake pads in (Carbotech XP8 again, really happy with them last year).
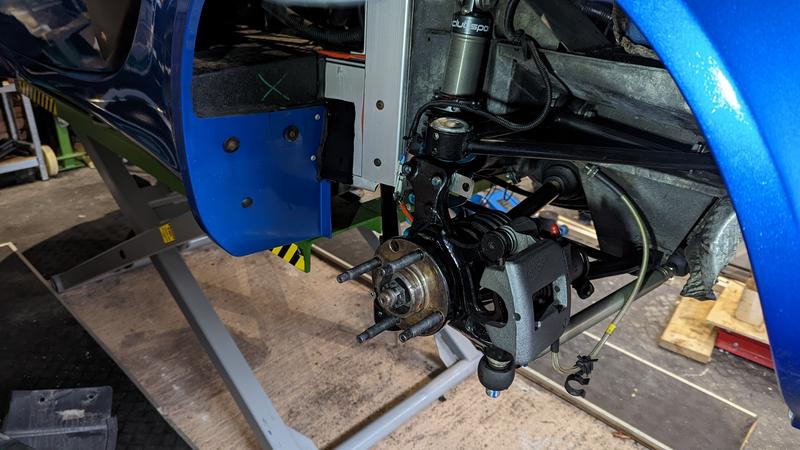
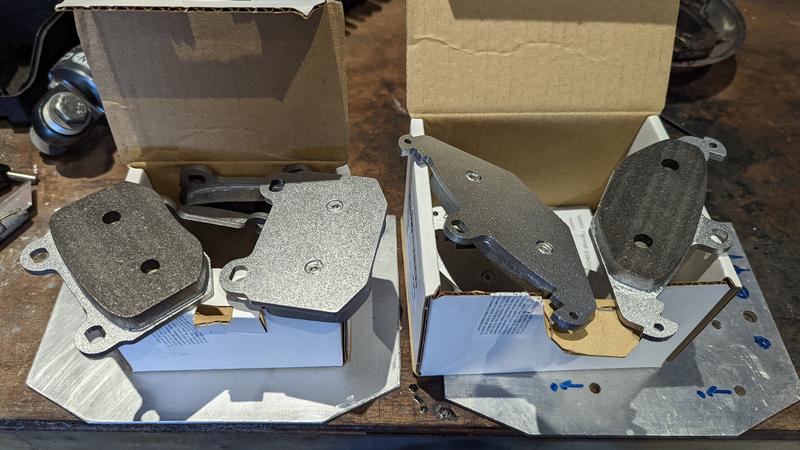
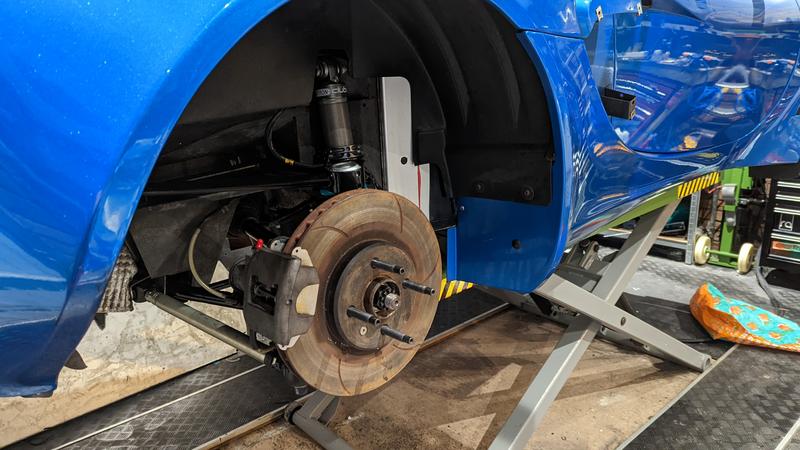
Wheels and undertrays even got a quick wash
Then finally it was time to lower the car on its wheels for the first time since end of December. My front rideheight was a little low, so a quick tweak on that got it roughly into a driveable stance. I’ll get this setup properly later in the week.
Topped and bled coolant after taking a shower in it whilst doing the gearbox cooler. No sign of any leaks, good news!
Then the moment of truth, long time readers may remember my last attempt to change a clutch fell a bit flat at this point as it wouldn’t disengage! Even though it was later identified as a rare/unlucky clutch issue, it haunts me. Getting the box back out at this stage is NOT fun. I was also a bit nervous about how ‘racey’ this new clutch was going to be, was I going to kangeroo out of the garage in a stink of clutch burn?!
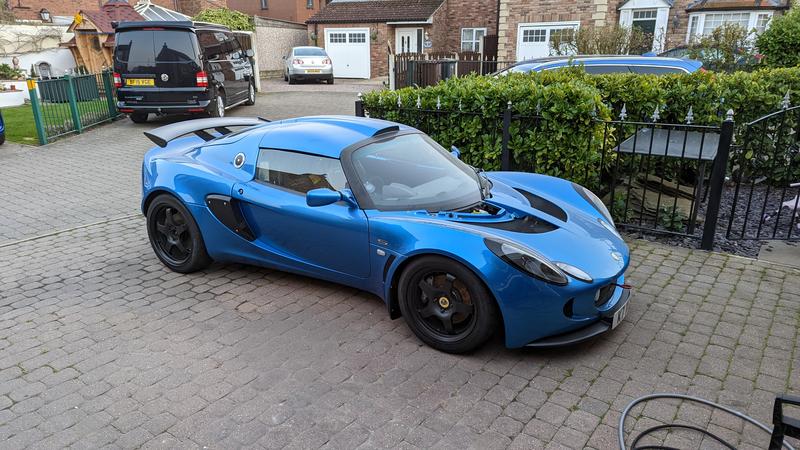
Answer? No - it pulled out of the garage like an OEM clutch would. No crunches, rattles, whistles or chatters - just a nice smooth engagement, and gentle manners at ‘carpark speeds’. I’ve not driven a car with a clutch since December, so it was particularly impressive. I took the car up and down the street, can select all gears with nothing feeling/sounding amiss yet, so fingers crossed.
All that remained was to wash off a Winters’ worth of garage and plaster dust.
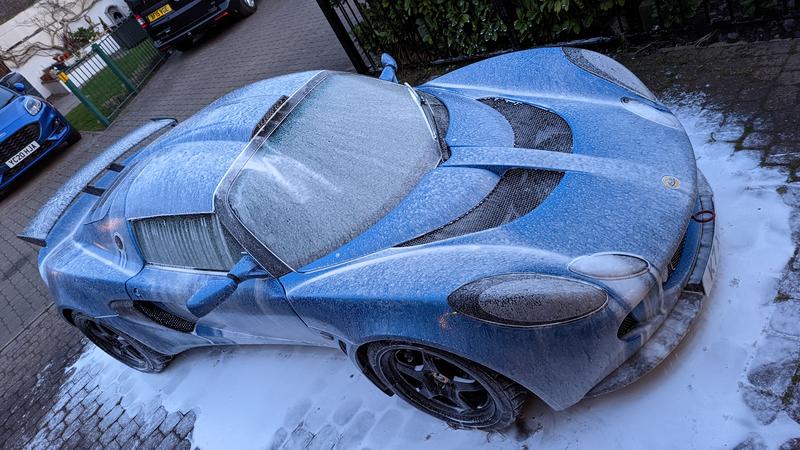
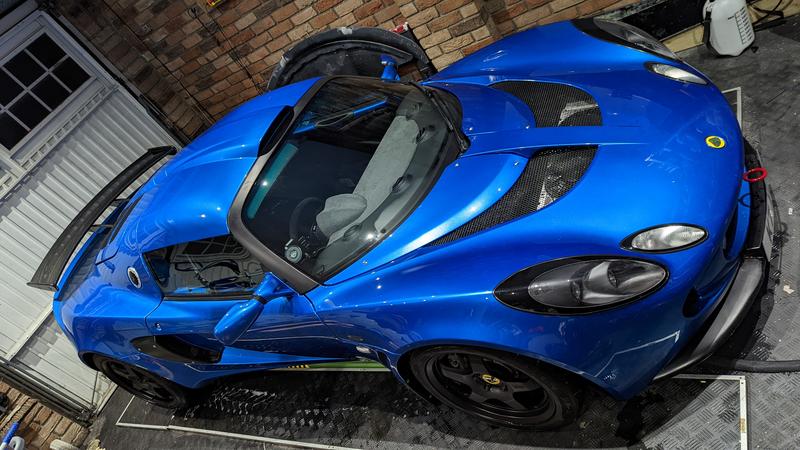
MOT later today, so fingers crossed for that.